Excavation work began for Burj Khalifa the tallest skyscraper
in the world in January 2004 and over the years, the building passed
many important milestones to become the tallest man-made structure the
world has ever seen. In just 1,325 days since excavation work started in
January, 2004, Burj Khalifa became the tallest free-standing structure
in the world.
www.abcgrouplive.com
World's Tallest Structure
Burj at Dubai - Now known as Burj Khalifa
The goal of the Burj Dubai Tower is not simply to be
the world's highest building: it's to embody the world's highest
aspirations. The superstructure has reached over 165 stories. The final
height of the building is 2,717 feet (828 meters). The height of the
multi-use skyscraper has "comfortably" exceed the previous record
holder, the 509 meter (1671 ft) tall Taipei 101.
The 280,000 m2 (3,000,000 ft2)
reinforced concrete multi-use Burj Dubai tower is utilized for retail, a
Giorgio Armani Hotel, residential and office. As with all super-tall
projects, difficult structural engineering problems needed to be
addressed and resolved.
Structural System Description
Burj
Khalifa has "refuge floors" at 25 to 30 story intervals that are more
fire resistant and have separate air supplies in case of emergency. Its
reinforced concrete structure makes it stronger than steel-frame
skyscrapers.
Designers purposely shaped the structural concrete
Burj Dubai - "Y" shaped in plan - to reduce the wind forces on the
tower, as well as to keep the structure simple and foster
constructibility. The structural system can be described as a
"buttressed" core (Figures 1, 2 and 3). Each wing, with its own high
performance concrete corridor walls and perimeter columns, buttresses
the others via a six-sided central core, or hexagonal hub. The result is
a tower that is extremely stiff laterally and torsionally. SOM applied a
rigorous geometry to the tower that aligned all the common central
core, wall, and column elements.
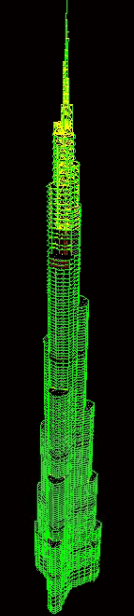
The setbacks are organized such that the Tower's
width changes at each setback. The advantage of the stepping and shaping
is to "confuse the wind'1. The wind vortices never get organized
because at each new tier the wind encounters a different building shape.
The Khalifa's Tower and Podium structures are currently under
construction (Figure 3) and the project is scheduled for topping out in
2008.
Burj's Architectural Design
The context of the Burj Dubai being located in the city of Dubai, UAE, drove the inspiration for the building form to incorporate cultural, historical, and organic influences particular to the region.Structural Analysis and Design Facts
The center hexagonal reinforced concrete core walls
provide the torsional resistance of the structure similar to a closed
tube or axle. The center hexagonal walls are buttressed by the wing
walls and hammer head walls which behave as the webs and flanges of a
beam to resist the wind shears and moments.
Outriggers at the mechanical floors allow the columns
to participate in the lateral load resistance of the structure; hence,
all of the vertical concrete is utilized to support both gravity and
lateral loads. The wall concrete specified strengths ranged from C80 to
C60 cube strength and utilized Portland cement and fly ash.
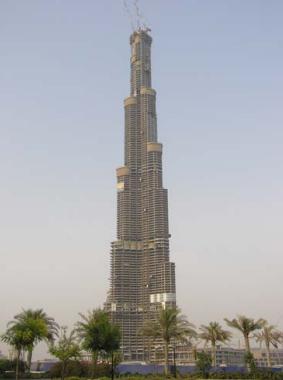
The wall thicknesses and column sizes were fine-tuned
to reduce the effects of creep and shrinkage on the individual elements
which compose the structure. To reduce the effects of differential
column shortening, due to creep, between the perimeter columns and
interior walls, the perimeter columns were sized such that the
self-weight gravity stress on the perimeter columns matched the stress
on the interior corridor walls.
The five (5) sets of outriggers, distributed up the
building, tie all the vertical load carrying elements together, further
ensuring uniform gravity stresses: hence, reducing differential creep
movements. Since the shrinkage in concrete occurs more quickly in
thinner walls or columns, the perimeter column thickness of 600mm (24")
matched the typical corridor wall thickness (similar volume to surface
ratios) (Figure 5) to ensure the columns and walls will generally
shorten at the same rate due to concrete shrinkage.
The top section of the Tower consists of a structural steel
spire utilizing a diagonally braced lateral system. The structural
steel spire was designed for gravity, wind, seismic and fatigue in
accordance with the requirements of AISC Load and Resistance Factor
Design Specification for Structural Steel Buildings (1999). The exterior
exposed steel is protected with a flame applied aluminum finish.
Analysis for Gravity
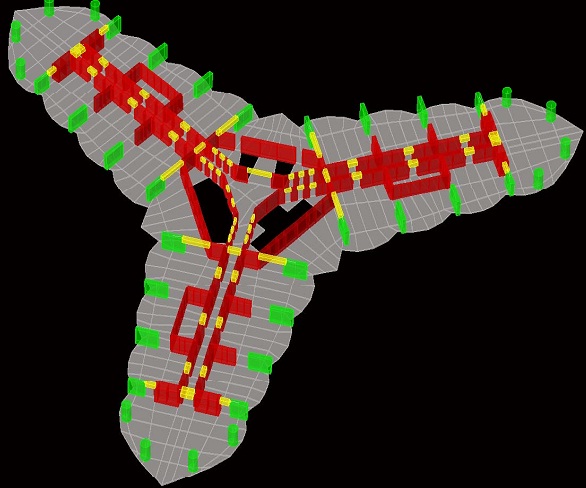
Site Test and Analysis
The Dubai Municipality (DM) specifies Dubai as a
UBC97 Zone 2a seismic region (with a seismic zone facior Z = 0.15 and
soil profile Sc). The seismic analysis consisted of a site specific
response spectra analysis. Seismic loading typically did not govern the
design of the reinforced concrete Tower structure. Seismic loading did
govern the design of the reinforced concrete Podium buildings and the
Tower structural steel spire.
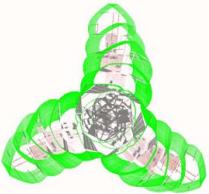
Burj Khalifa's Foundations and Site Conditions
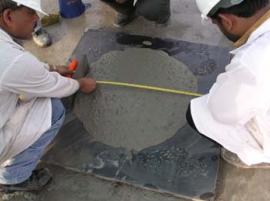
The Burj Tower raft is supported by 194 bored
cast-in-place piles. The piles are 1.5 meter in diameter and
approximately 43 meters long with a design capacity of 3,000 tonnes
each. The Tower pile load test supported over 6,000 tonnes (Figure 12).
The C60 (cube strength) SCC concrete was placed by the tremie method
utilizing polymer slurry. The friction piles are supported in the
naturally cemented calcisiltite conglomeritic calcisiltite fomiations
developing an ultimate pile skin friction of 250 to 350 kPa (2.6 to 3.6
tons / ft ). When the rebar cage was placed in the piles, special
attention was paid to orient the rebar cage such that the raft bottom
rebar could be threaded through the numerous pile rebar cages without
interruption, which greatly simplified the raft construction.
The site geotechnical investigation consisted of the following Phases:- Phase I; 23 Boreholes (three with pressuremeter testing) with depths up to 90m.
- Phase 2: 3 Boreholes drilled with cross-hole geophysics.
- Phase 3: 6 Boreholes (two with pressure meter testing) with depths up to 60m.
- Phase 4: 1 Borehole with cross-hole and down-hole gophysics; depth = 140m
3D foundation settlement analysis
A detailed 3D foundation settlement analysis was
carried out (by Hyder Consulting Ltd., UK) based on the results of the
geotechnical investigation and the pile load test results. It was
determined the maximum long-term settlement over time would be about a
maximum of 80mm (3.1"). This settlement would be a gradual curvature of
the top of grade over the entire large site. When the construction was
at Level 135, the average foundation settlement was 30mm (1.2"). The
geo-technical studies were peer reviewed by both Mr. Clyde Baker of STS
Consultants, Ltd. (Chicago, IL, USA) and by Dr. Harry Poulos of Coffey
Geosciences (Sydney, Australia).
The groundwater in which the Burj Dubai substructure
is constructed is particularly severe, with chloride concentrations of
up to 4.5%, and sulfates of up to 0.6%. The chloride and sulfate
concentrations found in the groundwater are even higher than the
concentrations in sea water. Accordingly, the primary consideration in
designing the piles and raft foundation was durability. The concrete mix
for the piles was a 60 MPa mix based on a triple blend with 25% fly
ash, 7% silica fume, and a water to cement ratio of 0.32. The concrete
was also designed as a fully self consolidating concrete, incorporating a
viscosity modifying admixture with a slump flow of 675 +/- 75mm to
limit the possibility of defects during construction.
Due to the aggressive conditions present caused by
the extremely corrosive ground water, a rigorous program of
anti-corrosion measures was required to ensure the durability of the
foundations. Measures implemented included specialized waterproofing
systems, increased concrete cover, the addition of corrosion
inhibitors to the concrete mix. stringent crack control design
criteria, and cathodic protection system utilizing titanium mesh (Figure
13) with an impressed current.
Wind Engineering
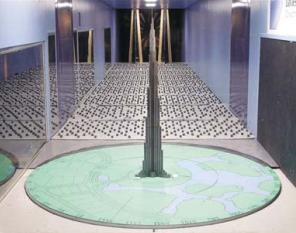
The wind tunnel program included rigid-model force
balance tests, a foil multi degree of freedom aero elastic model
studies, measurements of localized pressures, pedestrian wind
environment studies and wind climatic studies. Wind tunnel models
account for the cross wind effects of wind induced vortex shedding on
the building. The aeroelastic and force balance studies used models
mostly at 1:500 scale. The RWDI wind engineering was peer reviewed by
Dr. Nick Isyumov of the University of Western Ontario Boundary Layer
Wind Tunnel Laboratory.
No comments:
Post a Comment